Why is the number of teeth on saw blade milling cutters so important?
The number of teeth on saw blade milling cutters is a core parameter that determines processing efficiency, surface quality and tool life. Choosing the wrong number of teeth may cause material burrs, tool overheating and even chipping. This article will explain the five major effects of the number of teeth on cutting and provide a guide to selecting the number of teeth on saw blade milling cutters to help you optimize your processing process.
1. How does the number of teeth affect cutting efficiency?
More teeth (dense teeth): more cutting edges are involved in cutting per unit time, suitable for fine machining and soft materials (such as aluminum, plastic), can quickly remove materials and reduce processing time. Fewer teeth (sparse teeth): single tooth cutting force is greater, suitable for rough machining of hard materials (such as stainless steel, titanium alloy), avoiding tool wear caused by poor heat dissipation. Industry data: Tests show that when machining aluminum alloys, 40-tooth milling cutters are 30% more efficient than 24-tooth milling cutters, but stainless steel milling cutters need to be reduced to 16-20 teeth to extend life.
2. The relationship between the number of teeth and processing quality
3. Chip removal and heat dissipation: the invisible key to tooth number design
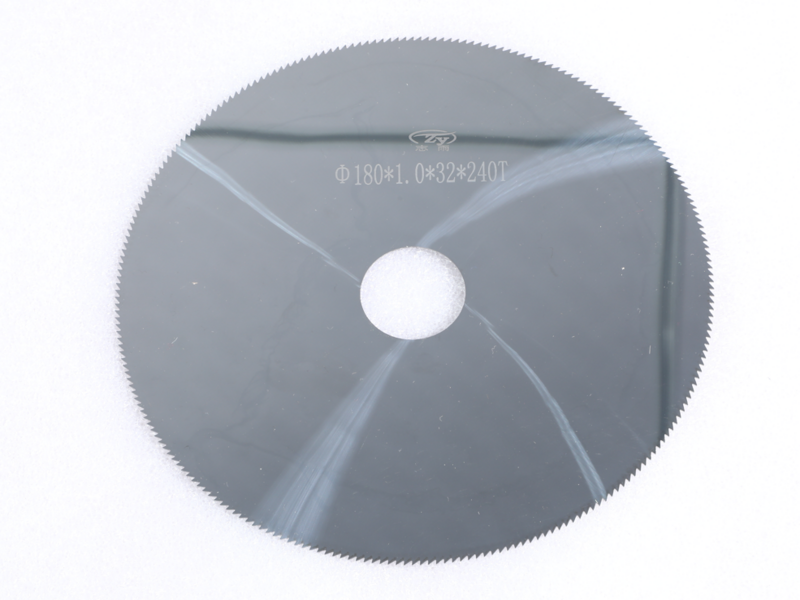
4. Tool life: cost game of tooth number selection
Close-tooth challenges: Too little cutting volume per tooth will increase friction and wear. When processing hardened steel, the speed needs to be increased but the feed needs to be reduced. Sparse-tooth applicable scenarios: Under heavy-load cutting, a reasonable reduction in the number of teeth can disperse the load and extend the overall life. Data comparison: When processing mold steel, the life of a 24-tooth milling cutter is twice that of a 40-tooth milling cutter, but it sacrifices 30% of the processing speed.
5. How to choose the best number of teeth? 3-step decision-making method
Evaluate material properties: choose dense teeth for soft materials, and sparse teeth for hard/sticky materials. Identify the processing stage: use low teeth for fast material removal in roughing, and high teeth for smooth finish in finishing. Match cutting parameters: high teeth require lower feed per tooth (fz), sparse teeth can increase fz but vibration needs to be monitored.
Summary: Gear selection strategy to balance efficiency and precision
When choosing the number of teeth on a saw blade milling cutter, you need to weigh the material hardness, processing stage, equipment rigidity and cost. Close teeth improve efficiency and accuracy, while sparse teeth enhance chip removal and durability. It is recommended to save this guide and flexibly adjust it according to actual working conditions.
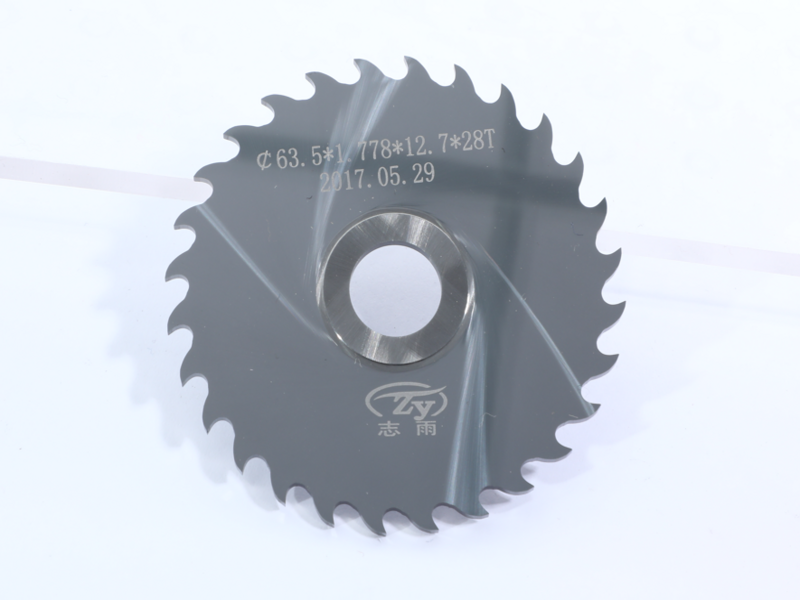