Chamfer milling cutters are indispensable tools in mechanical processing, and their performance directly affects processing efficiency, surface quality and cost control. This article will analyze how to scientifically select chamfer milling cutters from two core dimensions: number of blades design (4 blades vs. 2 blades) and coating technology (blue nano HRC65 vs. bronze HRC55).
1. Comparison and selection of 4-edge chamfering milling cutter and 2-edge chamfering milling cutter
1.1. Cutting efficiency and processing scenarios
4-edge chamfering cutter: The four-edge design significantly improves efficiency through multi-edge synchronous cutting, which is especially suitable for batch processing of high-hardness materials (such as hardened steel and titanium alloy). It removes more material per unit time and can shorten the processing cycle by about 30%-50%. However, the multi-edge structure may lead to insufficient chip removal space, and a high-pressure cooling system is required to optimize the chip removal effect.
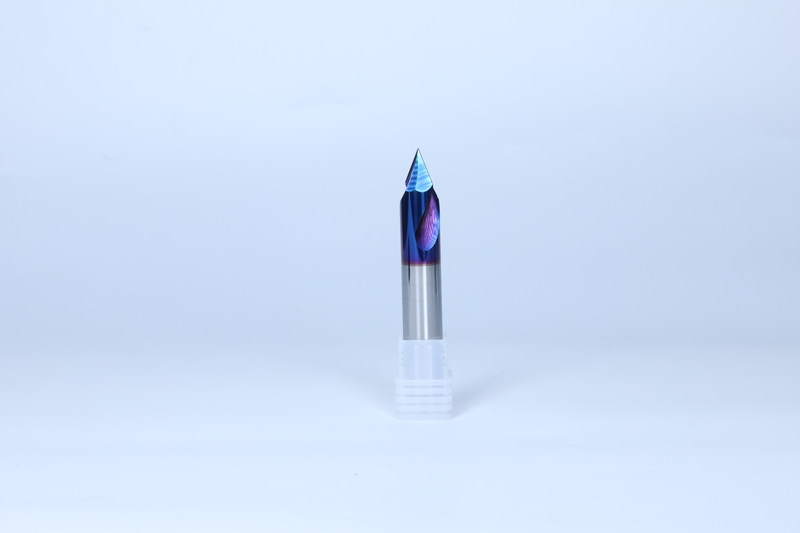
1.2. Surface quality and tool life
4-edge cutter:Multi-edge synchronous cutting is prone to vibration, and improper parameter setting may cause surface scratches. However, through the blue nano HRC65 coating technology, the friction coefficient can be effectively reduced, the surface roughness defects can be compensated, and the tool life can be extended to twice that of ordinary coatings.
2-edged knife: The cutting process is more stable and suitable for scenes with high finish requirements. However, due to the concentrated force on the single edge, the wear rate is fast and the blade needs to be replaced frequently. The bronze HRC55 coating version is more suitable for light-load processing of medium and low hardness materials.
1.3. Applicable materials and cost control
4-edged knife: It is preferred for high-hardness materials (HRC45+) in aerospace and automobile manufacturing, and the unit price is higher (for example, the price of the HRC65 blue nano-coated 4-edged knife is about 20%-30% higher than that of the bronze coating).
2-edged knife: An economical choice, suitable for soft materials such as aluminum and stainless steel. The bronze HRC55 coating version is more affordable
2. Performance Differences between Blue Nano HRC65 and Bronze HRC55 Coatings
2.1. Wear resistance and processing hardness
Blue Nano HRC65 coating:Adopting nano-level multi-layer composite coating technology, the hardness can reach above HV3200, and supports the processing of super-hard materials below HRC65 (such as mold steel and high-temperature alloys). It has excellent high-temperature resistance, and the continuous cutting temperature can reach 800℃ without failure, and the service life is 40%-60% longer than that of bronze coating.
Bronze HRC55 coating: Suitable for medium-hardness materials below HRC55 (such as carbon steel and alloy steel), the coating thickness is thinner (about 2-3μm), and the cost is lower, but the coating is prone to peeling due to heat accumulation during continuous processing.
2.2. Cutting performance and surface treatment
Blue Nano coating:The friction coefficient is as low as 0.25, which can reduce cutting heat and built-up edge and improve finish. It is especially suitable for high-speed processing (recommended line speed 150-200m/min), and the 4-edge design can achieve efficient finishing.
Bronze coating: The friction coefficient is about 0.45, which is suitable for medium and low speed processing (line speed 80-120m/min), and the economy is outstanding, but the feed rate needs to be reduced to avoid excessive wear of the coating.
2.3. Economy and applicable scenarios
Blue Nano HRC65: The unit price is higher (for example, the price of a 4-edged knife with a diameter of 10mm is about 113.5 yuan), but the single processing cost is lower, which is suitable for long-term mass production.
Bronze HRC55: The price advantage is obvious (30%-50% lower than Blue Nano for the same specification), which is suitable for small and medium batches or cost-sensitive projects.
3. Comprehensive purchase suggestions
3.1High hardness materials + high efficiency requirements:
choose 4-edge blue nano HRC65 coated chamfering cutters, such as processing hardened steel or titanium alloy parts.
3.2 Precision processing + soft materials
2-edge bronze HRC55 coating is preferred, suitable for chamfering aluminum molds or electronic components. Limited budget + medium load: 4-edge knives with bronze HRC55 coating can balance cost and efficiency, suitable for batch processing of carbon steel parts.
3.3 Complex working conditions combination:
It is recommended to equip with multi-specification tools, such as using 4-edge blue nano knives for rough processing, and then changing to 2-edge knives for fine edge trimming.